Connected data for improved efficiency of bolt torquing operations offshore
EDPR is seeking a solution that will speed up the process of securing the bolted connection, ensure the correct tension is achieved for each bolt and improve the QHSE during this process.
Opportunity
Challenge opens
12/03/2019
Challenge closes
03/05/2019
Benefit
Background
EDPR currently operates, develops and builds a number of wind farms around the world. The OWiX initiative is supporting EDPR to identify transferable solutions to its innovation challenges.
During installation of an offshore wind turbine, upwards of 1000 bolts are used to secure its components in place. Most wind farms to date have used cylindrical pile foundations called monopiles. A typical design deploys a concrete grout between the monopile and the yellow transition piece that sits on top of the foundation. Due to historical issues with this type of connection a number of wind farms (e.g. Borkum Riffgrund 2 and Gemini) have instead used bolted connections to secure the transition piece to a flange welded to the top of the monopile using approximately 120 bolts.
The process for securing this connection is critical to the success of the project; the robustness of the connection is crucial in the long term and the speed, fluency and safety of the bolt tensioning and measurement operation during the installation phase has large cost implications for the installation package (due to the fact that this activity is carried out on the critical path of the installation vessel).
EDPR is seeking a solution that will speed up the process of securing the bolted connection, ensure the correct tension is achieved for each bolt and improve the QHSE during this process. The final solution may also have applicability in the operation and maintenance (O&M) phase of operational wind farms, where during routine checks, each bolt is subject to tension checks. Remote monitoring of the tensions in the bolted connections is optimal to reduce cost, time and risks associated with visiting offshore wind turbines.
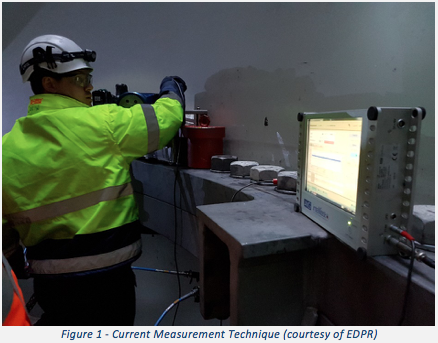
Whilst not limiting the technologies from solution providers, it is expected that solutions would consider innovations from some of the following areas:
- Self-lifting and heavy-lifting technology
- Robotics and mechatronics
- Naval architecture
- Data analytics
- Internet of Things
- Aerospace engineering and manufacturing
- Automotive assembly and manufacture
- Heavy engineering and manufacturing
- Artificial intelligence
- Existing O&M service providers with new ideas
- Collaborations between service and technology providers
To meet the desired timescale and risks, it is preferred that the proposed solution, or the key part(s) of the solution, has been commercially proven in other sectors or within a test program which includes offshore conditions (for both installation and operation) trials.
Rewards and benefits
Successful applicants will be given an opportunity to pitch to EDPR. The package may also include:
- Support from the ORE Catapult or the KTN
- Support in the development of a prototype or pilot
- Technical support
- A place in KTN or ORE Catapult events
- A potential business collaboration
- Investor introductions (if investment is required)
Solution Requirements
Functional Requirements
- The bolts are tightened in defined sequences, which are determined at the design stage. This sequence must be followed when tightening the bolts.
- Current approaches include a team of men placed inside the transition piece on its lower deck, tightening the bolt with heavy, manually operated torque wrenches, often with more than one torque wrench in use at a time. During the tightening of the bolts, an ultrasonic measurement device (secured to the bolt head or tip) is used to check the tension. Whilst the final tension levels in the bolts are fixed by the designer of the connection, both the technology used to tighten and measure the bolts, as well as the bolt tightening sequence, could change.
- The process is slowed by a lack of efficiency in the interconnectivity of the torque wrenches and the measurement device, where data must manually be gathered on the spot by an engineer and then analysed before further action (e.g. re-tightening bolts) is taken.
- The current process involves a large number of tools and people and can lead to an untidy workplace. New solutions should seek to overcome this.
- During operation a wind turbine a similar process may also need to be undertaken. Under the stresses of the environment, each bolt can suffer from a loosening or relaxation effect. This places a requirement on the wind farm operator to send a technician to check the bolts individually to check each bolt is set at the correct tension. Each bolt may need to be re-tightened. Due to the elastic response of the bolted connection, the tightening of a single bolt can influence the tension levels in the other bolts. Therefore, all bolts need to be checked on each occasion, resulting in a long and laborious process.
- Current methods for measurement of the tension include products which have both hardware and software solutions for an individual bolt but do not take into account readings from a sequence of bolts. A new solution should seek to understand the whole process, connect this data in a more intelligent way, looking at a component-to-component connection holistically, speed up the measurement and analysis process and feed it back to the technicians for them to infer new actions.
- A solution could be a pocket-sized or robotic tool that could measure the tension post release. This data could then feed into a tablet device, used by the technicians to then use multiple torque wrenches. ?
- The proposed solutions for this challenge must be deployable without requiring major changes to existing manufacturing and design of offshore wind turbines. Major changes would result in significant cost or time to the fabrication/installation process which is not recovered by the savings from the new solution.
- The final solution could be adapted for use in both new build sites and operational sites, and therefore will need to be applicable to different types and makes of turbines.
Technical Characteristics
- Solutions should enable handheld contact inspection of torque, ideally recorded via a connection to a PC or tablet. This should aim to allow the user to map and asses a ring of bolts and provide an ongoing monitoring capability by keeping records of each bolt. It should also contain a connection to a data recording device and record data.
- Either torque or tension could be applied to tighten the bolts. This is wind farm design dependent.
- Typically, the bolts to be measured and tightened range from size M56 to M72.
- A solution should be able to record and build up maintenance and historical data for the turbines tested and ideally provide analytical tools to help predict future campaigns.
- Torque wrenches currently in use are mechanical with no digital input, however some hydraulic pumps that drive these tools have the ability for a serial input.
- Measurement tools currently in use are digital and contain two USB ports for connections to a Windows tablet. Typically, multiple measurement tools are used to gather data and these are manually collected onto a single device before being analysed in Excel (CSV file). New solutions should seek to automate this process using wireless connections to multiple measurement devices.
- Tablets or devices used should be heavy duty and highly dirt and humidity resistant. The same applies to any connection cables.
- For an 8MW turbine, there are roughly 120 M48 bolts on the monopile top flange to measure and tighten to a minimum allowable torque of approximately 2100-2300kN and a maximum acceptable torque of approximately 2500kN.
- Current solutions have used nuts and bolts but a threaded flange could also be proposed on future foundation designs.
- Currently technicians work in 12 hour shifts, enabling 24 hour campaigns.
- The ability for technicians to operate the solution using gloves is a benefit.
Operating Conditions
- The device must be capable of working in offshore conditions with full weatherproofing, where off-the-shelf consumer electronics do not tend to withstand the harsh offshore conditions.
- Solutions must be able to be operated safely and reliably in offshore conditions of:
- Up to 12m/s wind speeds
- 1-2m wave heights
- Ambient temperatures of -10C to +40C
- Dirty and dusty environments
Deployment Timescale
- Launch of the Competition: 12 March 2019
- Deadline for applications: 30 April 2019
- Selection and notification of finalists: 31 May 2019
- Solutions should be:
- Fully deployable for prototype testing within 6 months of competition win.
- Full commercial deployment by the end of 2019 (there are operational sites that a solution could start work on immediately if the system is already commercially available).
Eligibility and assessment criteria
Entrants to this competition must be:
- Established businesses, startups, SMEs or individual entrepreneurs
- UK based or have the intention to set up a UK base
Applications will be assessed on:
- Relevance to the topic
- Innovative nature of the subject
- Coherence of the proposed business model
- Feasibility/ economic viability
- Development potential
- Maturity of project/solution
- Ability to launch project quickly/Ease of implementation
- Price/quality ratio
- Suitability for the UK Market (inc. building regulations and certification etc.).
Cost Requirement and Market Size
- Current solutions demand a tightening campaign taking upwards of 50 hours per structure until the technician team has implemented its learning. Subsequent campaigns typically take around 24 hours per structure. The cost of a vessel is approximately £150-250k per day so this is the biggest cost driver during a campaign. New solutions should seek to reduce the average campaign to 12 hours per foundation or better.
IP and Potential Commercial Route
- Existing background IP associated with a potential solution will remain with Solution Provider(s). Where any new IP generation is envisaged, it will be subject to the mutual IP agreement of the Solution Provider(s) and Innovation Challenger.
- Any commercial deployment of transferred solution or newly developed solution, through licensing, joint venture, partnership or direct investment, will be subject to the commercial agreement between the Solution Provider(s) and Innovation Challenger.
- Where necessary, a non-disclosure agreement (NDA) may be signed to uphold confidentiality in the engagement between the Solution Provider(s) and Innovation Challenger.
- Innovate UK and KTN do not take any share of IP ownership or enter into commercial venture through the OWiX programme.
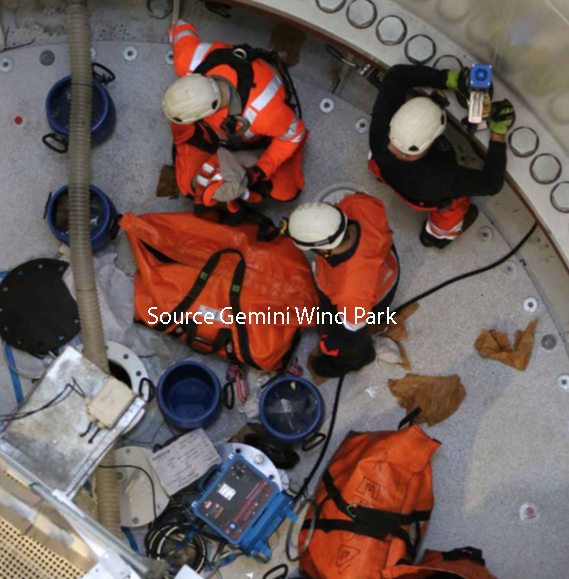
This challenge is brought to you by:
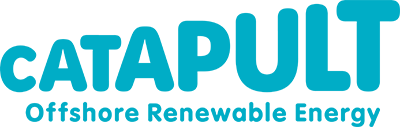
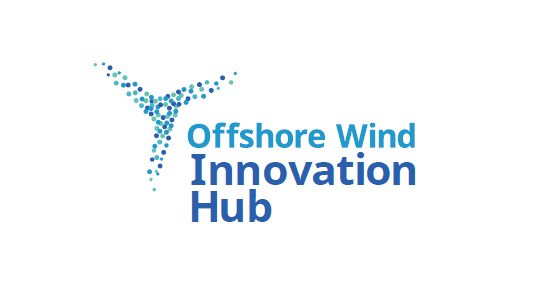
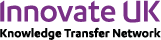